Trong ngành sản xuất công nghiệp hiện đại, máy chiết rót đóng vai trò then chốt trong quy trình đóng gói sản phẩm dạng lỏng. Hiểu rõ về cấu tạo và chức năng của từng bộ phận không chỉ giúp tối ưu hóa quá trình sản xuất mà còn đảm bảo chất lượng sản phẩm đầu ra.
Với kinh nghiệm trong lĩnh vực phân phối thiết bị công nghiệp, VITEKO sẽ phân tích chi tiết về 5 bộ phận quan trọng nhất của máy chiết rót, giúp người dùng có cái nhìn tổng quan và chuyên sâu về thiết bị này.
I. Chi tiết về 5 bộ phận quan trọng nhất của máy chiết rót
Trong cấu tạo của một máy chiết rót công nghiệp, mỗi bộ phận đều có vai trò riêng biệt nhưng lại có mối liên hệ chặt chẽ với nhau. Hãy cùng tìm hiểu chi tiết về từng bộ phận quan trọng.
1. Bình chứa (Storage Tank)
Bình chứa là thành phần cốt lõi của máy chiết rót, đóng vai trò dự trữ và cung cấp nguyên liệu cho toàn bộ hệ thống. Thiết kế của bình chứa tuân theo tiêu chuẩn kỹ thuật nghiêm ngặt nhằm đảm bảo chất lượng sản phẩm.
Về cấu tạo, bình chứa được chế tạo từ thép không gỉ SUS304 hoặc SUS316L, đảm bảo độ bền và khả năng chống ăn mòn cao. Thành bình được thiết kế hai lớp với lớp cách nhiệt, giúp duy trì nhiệt độ ổn định cho nguyên liệu.
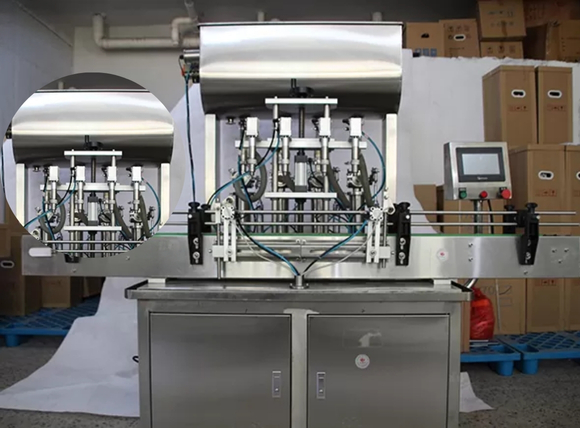
Bình chứa hiện đại được trang bị các tính năng đặc biệt như cảm biến mức chất lỏng, hệ thống kiểm soát nhiệt độ tự động và van xả áp an toàn. Đặc biệt, hệ thống CIP (Clean-In-Place) tích hợp cho phép vệ sinh bình chứa mà không cần tháo rời.
Về tiêu chuẩn vệ sinh, bình chứa phải đáp ứng các yêu cầu GMP và HACCP. Bề mặt tiếp xúc với sản phẩm được đánh bóng với độ nhám Ra ≤ 0.8μm, ngăn ngừa tích tụ cặn và vi sinh vật.
2. Hệ thống bơm (Pump System)
Hệ thống bơm đóng vai trò quyết định trong việc vận chuyển và định lượng chất lỏng chính xác. Với công nghệ hiện đại, các loại bơm công nghiệp được thiết kế phù hợp với từng loại sản phẩm cụ thể.
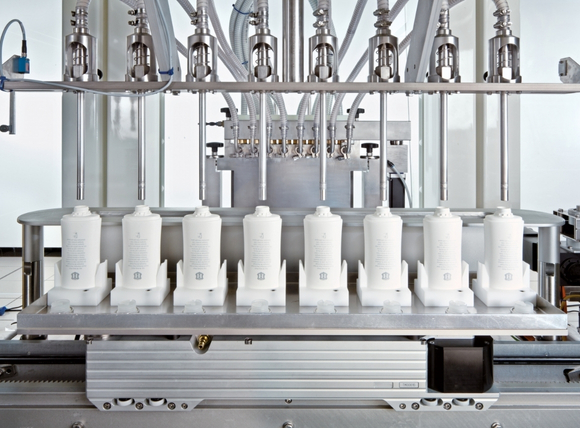
Trong công nghiệp, ba loại bơm phổ biến là bơm màng, bơm bánh răng và bơm piston. Mỗi loại có những ưu điểm riêng: bơm màng phù hợp với sản phẩm nhớt cao, bơm bánh răng cho độ ổn định tốt, còn bơm piston mang lại độ chính xác cao nhất.
Nguyên lý hoạt động của hệ thống bơm dựa trên sự kết hợp giữa áp suất và lưu lượng. Động cơ servo điều khiển tốc độ bơm, kết hợp với các van điều khiển để đảm bảo lưu lượng ổn định và chính xác đến 99.9%.
3. Vòi chiết (Filling Nozzles)
Vòi chiết là bộ phận trực tiếp định lượng sản phẩm vào bao bì. Cấu tạo của vòi chiết bao gồm thân vòi inox, đầu phun có thể điều chỉnh và hệ thống van điều khiển pneumatic.
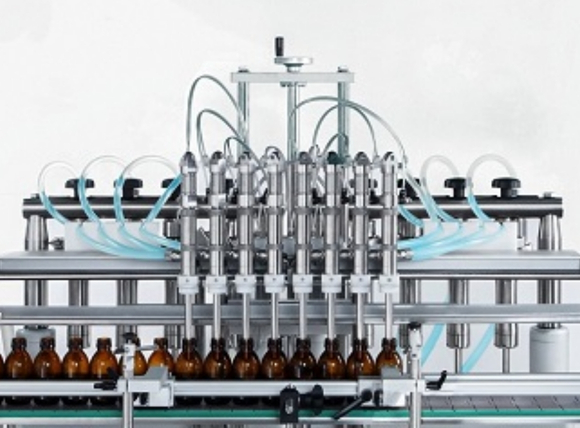
Công nghệ chống nhỏ giọt được tích hợp trong thiết kế vòi chiết thông qua cơ chế cut-off kép. Hệ thống này kết hợp giữa van điện từ tốc độ cao và cơ cấu cắt dòng cơ học, đảm bảo sản phẩm không bị nhỏ giọt sau khi kết thúc chu trình chiết.
Độ chính xác định lượng đạt được nhờ sự phối hợp giữa cảm biến áp suất, lưu lượng và thời gian. Hệ thống điều khiển PLC tự động điều chỉnh các thông số này để đảm bảo sai số không quá ±0.5% thể tích định mức.
4. Băng tải (Conveyor System)
Băng tải trong máy chiết rót công nghiệp được thiết kế đặc biệt để đảm bảo quá trình vận chuyển sản phẩm diễn ra trơn tru và chính xác. Hệ thống băng tải sử dụng vật liệu cao cấp như thép không gỉ 304/316 cho khung đỡ và nhựa thực phẩm FDA cho bề mặt băng.
Cấu tạo của hệ thống băng tải bao gồm mô-tơ servo chính xác cao, hệ thống dẫn động, con lăn định hướng và thanh dẫn hướng có thể điều chỉnh. Các cảm biến quang học được tích hợp tại các vị trí chiến lược để kiểm soát vị trí chai và đồng bộ hóa với các bộ phận khác.
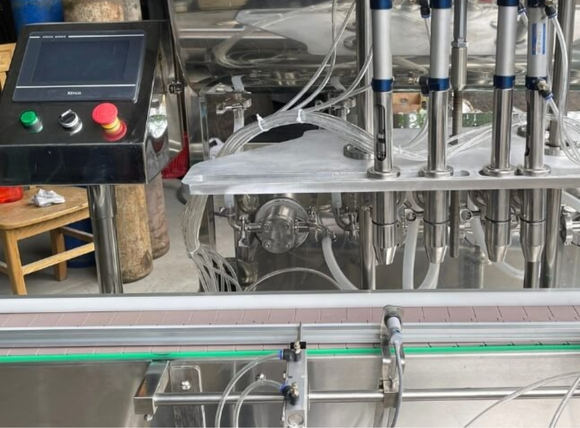
Tốc độ băng tải có thể điều chỉnh từ 1-100 m/phút thông qua biến tần kỹ thuật số. Hệ thống đồng bộ hóa tự động PLC đảm bảo tốc độ băng tải luôn phù hợp với tốc độ chiết rót, giúp tối ưu công suất sản xuất lên đến 24.000 chai/giờ.
Khả năng điều chỉnh kích thước linh hoạt cho phép thích ứng với nhiều loại chai khác nhau. Thanh dẫn hướng có thể điều chỉnh độ rộng từ 20mm đến 300mm, phù hợp với đa dạng kích cỡ bao bì.
5. Hệ thống điều khiển (Control System)
Hệ thống điều khiển là bộ não của máy chiết rót, tích hợp công nghệ PLC (Programmable Logic Controller) tiên tiến từ Siemens hoặc Mitsubishi. Vi điều khiển được lập trình để quản lý đồng thời nhiều thông số vận hành, đảm bảo độ ổn định và chính xác cao.
Giao diện người dùng (HMI) với màn hình cảm ứng công nghiệp 10-15 inch hiển thị trực quan các thông số vận hành. Menu đa ngôn ngữ cho phép người vận hành dễ dàng theo dõi và điều chỉnh các thông số như tốc độ chiết, thể tích, áp suất, nhiệt độ một cách nhanh chóng.
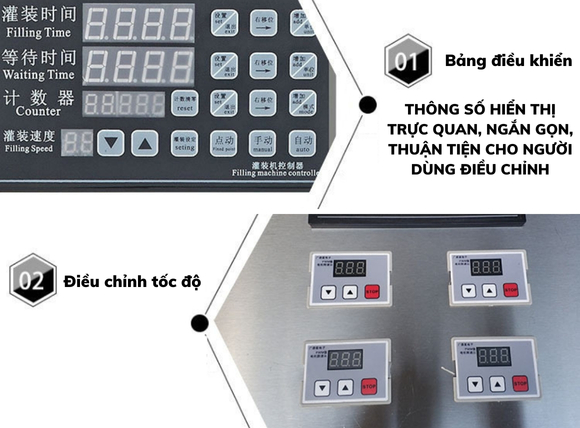
Các thông số được kiểm soát bao gồm lưu lượng (0.1-1000L/h), áp suất (0-10 bar), nhiệt độ (0-150°C), và tốc độ sản xuất (1.000-24.000 chai/giờ). Hệ thống tự động lưu trữ công thức sản xuất cho từng loại sản phẩm, giúp chuyển đổi nhanh chóng giữa các đơn hàng.
Tính năng an toàn và cảnh báo được tích hợp đầy đủ như dừng khẩn cấp, cảnh báo áp suất cao/thấp, cảnh báo nhiệt độ, mức chất lỏng và phát hiện kẹt chai. Hệ thống tự động ghi nhận và lưu trữ lịch sử vận hành, hỗ trợ công tác bảo trì và khắc phục sự cố.
Xem thêm:
II. Vai trò và sự tương tác giữa các bộ phận máy chiết rót trong quy trình sản xuất
Để hiểu rõ hơn về cách thức hoạt động của máy chiết rót công nghiệp, cần phân tích mối quan hệ giữa các bộ phận trong hệ thống. VITEKO sẽ phân tích chi tiết về vai trò và sự tương tác của từng thành phần.
1. Vai trò của từng bộ phận
Bình chứa (Storage Tank) đóng vai trò như một kho dự trữ nguyên liệu, duy trì nhiệt độ và áp suất ổn định cho quy trình sản xuất. Dung tích bình từ 100L đến 5000L tùy theo nhu cầu sản xuất. Cảm biến mức chất lỏng tích hợp giúp kiểm soát lượng nguyên liệu tự động.
Hệ thống bơm tạo ra động lực vận chuyển chất lỏng từ bình chứa đến vòi chiết với áp suất ổn định. Công suất bơm được điều chỉnh tự động từ 0.1-1000L/h dựa trên tín hiệu phản hồi từ cảm biến lưu lượng.
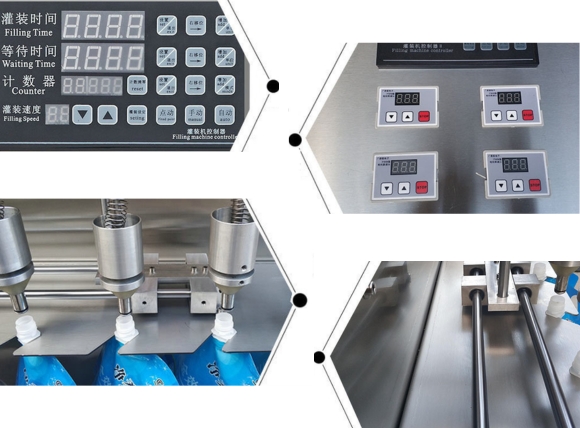
Vòi chiết thực hiện nhiệm vụ định lượng chính xác thể tích mong muốn vào bao bì. Độ chính xác đạt ±0.5% nhờ van điều khiển điện từ tốc độ cao, kết hợp với cơ cấu chống nhỏ giọt.
Băng tải đảm nhiệm chức năng vận chuyển và định vị chai chính xác dưới vòi chiết. Tốc độ băng tải đồng bộ hoàn toàn với tốc độ chiết rót, tối ưu công suất sản xuất.
Hệ thống điều khiển PLC đóng vai trò trung tâm, điều phối hoạt động của toàn bộ máy. Giao diện HMI trực quan giúp người vận hành dễ dàng kiểm soát và điều chỉnh các thông số.
2. Sự tương tác giữa các bộ phận máy chiết rót trong quy trình sản xuất
Quy trình hoạt động của máy chiết rót bắt đầu từ bình chứa, nơi nguyên liệu được duy trì ở nhiệt độ và áp suất tối ưu. Cảm biến mức chất lỏng liên tục gửi tín hiệu về hệ thống PLC, đảm bảo nguồn cung ổn định.
Hệ thống bơm hoạt động dựa trên tín hiệu từ cảm biến lưu lượng và áp suất. PLC tự động điều chỉnh công suất bơm để duy trì áp lực ổn định tại vòi chiết. Van điều áp tự động ngăn ngừa hiện tượng dao động áp suất.
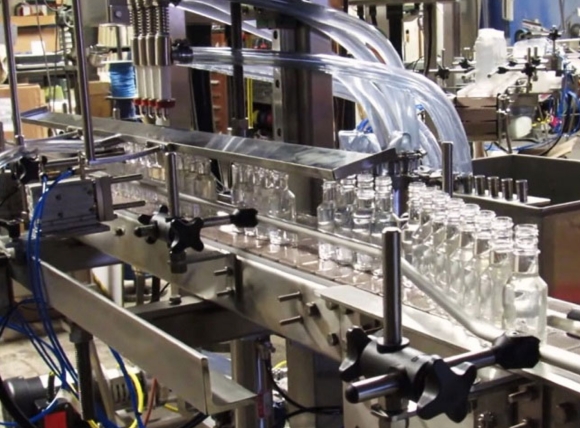
Băng tải vận chuyển chai dựa trên tín hiệu từ cảm biến quang học. Tốc độ băng tải được đồng bộ hóa với chu kỳ chiết rót thông qua bộ mã hóa vòng quay. Các cảm biến vị trí đảm bảo chai được định vị chính xác dưới vòi chiết.
Quá trình đồng bộ hóa hệ thống được thực hiện tự động qua PLC. Các thông số vận hành như tốc độ băng tải, thời gian mở van, áp suất bơm được tính toán và điều chỉnh theo thời gian thực để tối ưu hiệu suất sản xuất.
III. Hướng dẫn xử lý sự cố của các bộ phận
Trong quá trình vận hành máy chiết rót, việc nắm vững cách xử lý sự cố là yếu tố then chốt để duy trì hiệu suất sản xuất. VITEKO chia sẻ kinh nghiệm xử lý các vấn đề thường gặp và quy trình bảo trì hiệu quả.
1. Sự cố bình chứa và cách khắc phục
Bình chứa thường gặp một số sự cố như rò rỉ tại mối nối, áp suất không ổn định hoặc nhiệt độ dao động. Nguyên nhân chủ yếu đến từ gioăng phớt bị hỏng hoặc cảm biến sai lệch thông số.
Khi phát hiện rò rỉ tại mối nối, cần kiểm tra độ kín của gioăng và mức độ siết chặt bu-lông. Lực siết tiêu chuẩn cho bu-lông M10 là 45-50 Nm, M12 là 80-85 Nm. Thay thế gioăng nếu phát hiện dấu hiệu lão hóa hoặc biến dạng.
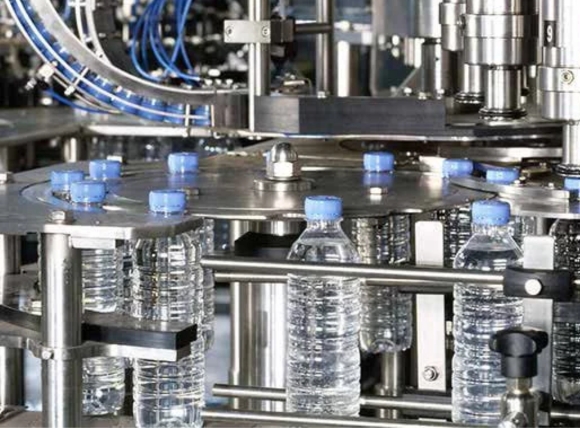
Tình trạng áp suất không ổn định thường liên quan đến van xả áp hoặc đồng hồ áp suất. Người vận hành cần hiệu chỉnh van xả áp theo thông số kỹ thuật, thường trong khoảng 2-6 bar tùy loại sản phẩm. Đồng hồ áp suất cần được kiểm định định kỳ 6 tháng/lần.
Vấn đề nhiệt độ dao động thường xuất phát từ cảm biến nhiệt hoặc hệ thống gia nhiệt. Hiệu chuẩn lại cảm biến theo quy trình của nhà sản xuất, đảm bảo sai số không quá ±1°C. Kiểm tra và vệ sinh điện trở gia nhiệt theo chu kỳ 3 tháng.
2. Xử lý vấn đề hệ thống bơm
Hệ thống bơm có thể xuất hiện tình trạng mất áp, rung động bất thường hoặc tiếng ồn cao. Phân tích nhanh các dấu hiệu giúp xác định chính xác nguyên nhân và phương án xử lý.
Mất áp thường do phớt bơm bị mòn hoặc không khí lọt vào đường ống. Kiểm tra và thay thế phớt bơm khi độ mòn vượt quá 0.5mm. Lắp đặt van xả khí tự động tại các điểm cao của đường ống để loại bỏ túi khí.
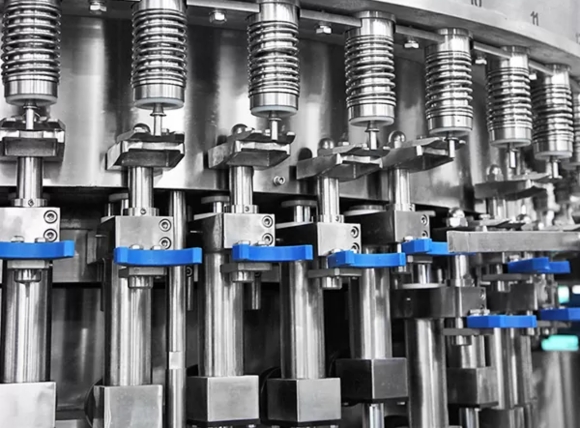
Rung động bất thường có thể do trục bơm lệch tâm hoặc ổ bi hỏng. Căn chỉnh độ đồng tâm giữa bơm và động cơ, sai số cho phép không quá 0.1mm. Thay thế ổ bi theo khuyến cáo của nhà sản xuất, thường sau 10.000 giờ hoạt động.
Tiếng ồn cao thường xuất hiện khi cavitation hoặc do các chi tiết bên trong bị mòn. Điều chỉnh áp suất hút để NPSHa lớn hơn NPSHr tối thiểu 0.5m. Kiểm tra độ mòn của cánh bơm và thân bơm, thay thế nếu độ mòn vượt quá giới hạn cho phép.
3. Khắc phục lỗi vòi chiết
Vòi chiết thường xuất hiện các vấn đề như nhỏ giọt, định lượng sai hoặc tắc nghẽn. Các sự cố này ảnh hưởng trực tiếp đến chất lượng sản phẩm và năng suất sản xuất.
Hiện tượng nhỏ giọt thường do van điện từ phản ứng chậm hoặc đệm làm kín bị hư hỏng. Kiểm tra thời gian đáp ứng của van điện từ, thông số tiêu chuẩn là 15-20 millisecond. Thay thế đệm làm kín nếu xuất hiện vết nứt hoặc biến dạng.
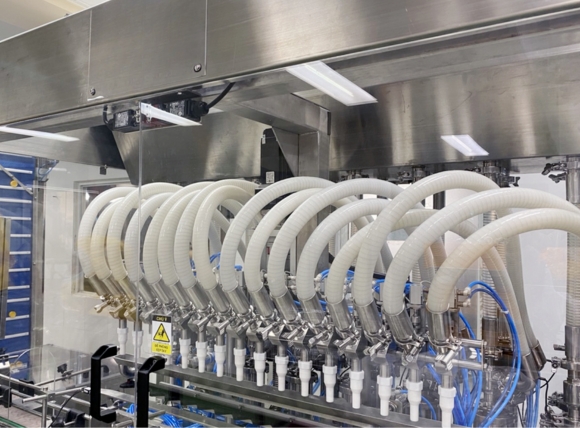
Định lượng sai có thể do áp suất không ổn định hoặc cảm biến lưu lượng bị nhiễu. Điều chỉnh van điều áp để duy trì áp suất ổn định trong khoảng ±0.1 bar. Hiệu chuẩn cảm biến lưu lượng theo quy trình của nhà sản xuất mỗi 3 tháng.
Tắc nghẽn vòi chiết có thể do cặn bám hoặc vật liệu lạ. Áp dụng quy trình CIP với dung dịch tẩy rửa chuyên dụng ở nhiệt độ 65-75°C trong 30 phút. Tháo rời và vệ sinh cơ học nếu cần thiết.
4. Xử lý sự cố hệ thống điều khiển
Hệ thống điều khiển có thể gặp lỗi màn hình, mất kết nối cảm biến hoặc chương trình bị treo. VITEKO đề xuất các giải pháp xử lý hiệu quả dựa trên kinh nghiệm thực tế.
Lỗi màn hình HMI thường do nguồn cấp không ổn định hoặc nhiễu điện từ. Lắp đặt bộ lọc nhiễu và ổn áp cho nguồn cấp, đảm bảo điện áp dao động trong khoảng ±10%. Kiểm tra và siết chặt các điểm nối mass.
Mất kết nối cảm biến có thể do đứt cáp hoặc nhiễu tín hiệu. Sử dụng thiết bị đo để kiểm tra tín hiệu analog 4-20mA hoặc tín hiệu số. Thay thế cáp tín hiệu nếu phát hiện hư hỏng, ưu tiên sử dụng cáp chống nhiễu.
Chương trình treo thường xảy ra do xung đột dữ liệu hoặc lỗi phần mềm. Sao lưu dữ liệu và cài đặt lại chương trình từ bản backup mới nhất. Cập nhật firmware theo khuyến cáo của nhà sản xuất.
5. Bảo trì và sửa chữa băng tải
Hệ thống băng tải đóng vai trò quan trọng trong việc vận chuyển sản phẩm, vì vậy cần được bảo trì định kỳ để đảm bảo hoạt động ổn định. Các vấn đề thường gặp bao gồm lệch băng, mòn con lăn hoặc động cơ quá tải.
Hiện tượng lệch băng thường do căn chỉnh không đúng hoặc tải không đều. Kiểm tra độ căng băng tải bằng dụng cụ đo lực căng, duy trì lực căng trong khoảng 15-20 N/mm chiều rộng băng. Điều chỉnh vị trí con lăn dẫn hướng để băng chạy thẳng.
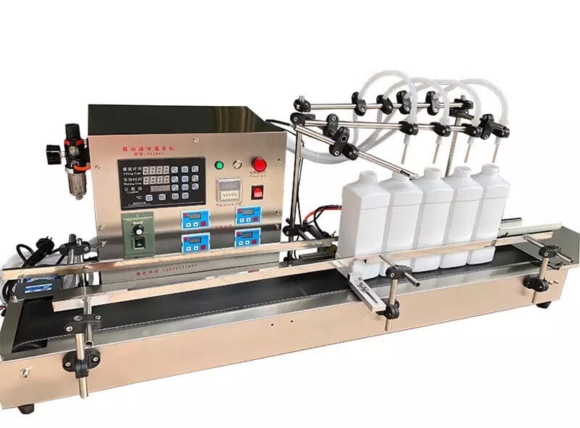
Con lăn bị mòn gây ra tiếng ồn và rung động bất thường. Đo đường kính con lăn tại các điểm khác nhau, thay thế khi độ mòn vượt quá 1mm. Bôi trơn ổ bi con lăn định kỳ bằng mỡ chịu nhiệt cấp NLGI 2.
Động cơ quá tải thường do ma sát tăng cao hoặc tải quá mức. Kiểm tra dòng điện tiêu thụ của động cơ, không được vượt quá 80% định mức. Vệ sinh và bôi trơn hệ thống truyền động để giảm ma sát.
6. Quy trình kiểm tra và bảo dưỡng định kỳ
VITEKO khuyến nghị áp dụng quy trình bảo dưỡng định kỳ để duy trì hiệu suất tối ưu cho máy chiết rót. Lịch trình bảo dưỡng được phân chia theo ngày, tuần và tháng với các công việc cụ thể.
Kiểm tra hàng ngày tập trung vào các thông số vận hành cơ bản: áp suất (2-6 bar), nhiệt độ (20-80°C), lưu lượng (±2%), độ rung động (<4.5mm/s). Ghi nhận các thông số vào nhật ký vận hành để theo dõi xu hướng thay đổi.
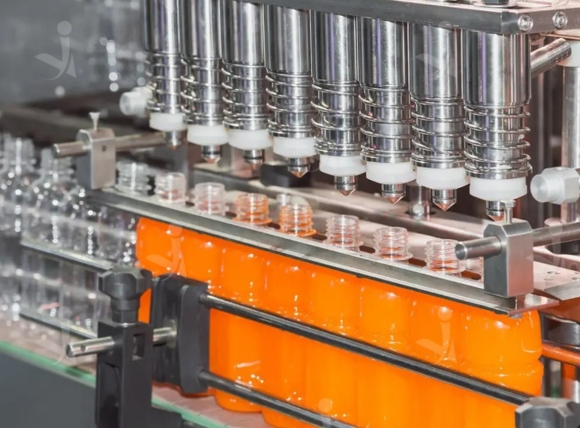
Bảo dưỡng hàng tuần bao gồm vệ sinh các bộ phận tiếp xúc với sản phẩm. Thực hiện quy trình CIP với dung dịch tẩy rửa chuyên dụng trong 30-45 phút. Kiểm tra độ kín của các mối nối và van bằng áp suất thử nghiệm 1.5 lần áp suất làm việc.
Bảo dưỡng hàng tháng tập trung vào kiểm tra và hiệu chuẩn các thiết bị đo lường. Hiệu chỉnh cảm biến lưu lượng với sai số cho phép ±0.5%. Kiểm định đồng hồ áp suất và nhiệt kế theo quy định của nhà sản xuất.
Tìm hiểu thêm:
Với kinh nghiệm trong lĩnh vực cung cấp thiết bị công nghiệp, VITEKO đã phân tích chi tiết về 5 bộ phận quan trọng nhất của máy chiết rót, bao gồm bình chứa, hệ thống bơm, vòi chiết, băng tải và hệ thống điều khiển. Mỗi bộ phận đóng vai trò riêng biệt nhưng có mối liên hệ chặt chẽ, tạo nên một hệ thống hoàn chỉnh với hiệu suất cao.
Để được tư vấn chi tiết về giải pháp máy chiết rót phù hợp với nhu cầu sản xuất, quý khách vui lòng liên hệ hotline 093 345 5566, đội ngũ chuyên viên kỹ thuật của VITEKO sẽ hỗ trợ tận tình nhất.
Tham khảo thêm các thiết bị máy móc thường được mua cùng
>>>Bấm vào ảnh để xem chi tiết các dòng máy chiết rót đang được bán tại VITEKO<<<